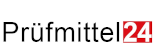
Eine Maßeinheit, in der Messtechnik auch Größeneinheit genannt, ist eine feststehende und vorher wohldefinierte Werteinheit, mit der die zu messende physikalische Größe der gleichen Art zum Zwecke des Messens verglichen wird.
Sichere Datenübertragung mit MarCom Professional
Weil Ihre Messergebnisse wertvoll sind: Unsere kostenlose Schnittstellensoftware MarCom Professional sorgt für die sichere, professionelle Übertragung Ihrer Messdaten an Ihre Windows-Anwendungen oder CAQ-Software.
Die Software ist kompatibel mit sämtlichen elektronischen Mahr-Messgeräten, die das flexible Schnittstellenkonzept MarConnect nutzen. Dazu gehören folgende Verbindungen:
Zum Download der Software: https://metrology.mahr.com/de/service/download-center/marcom-professional
Mit Maßlehren werden nur Außen- und Innenmaße geprüft.
Eine Maßverkörperung ist ein Messmittel, mit Hilfe dessen eine Maßeinheit verkörpert wird. Es besteht die Möglichkeit, entweder die ganze Einheit oder Teile davon oder aber die Einheit vervielfachend zu verkörpern. Zu den Maßverkörperungen sind in der Längenprüftechnik neben Endmaßen, Strichmaßen, Messgewinden, Wellenlängen des Lichtes auch die Lehren zu zählen.
Grundsätzlich ist es nicht möglich exakt zu messen. Durch eine Vielzahl physikalischer Einflussfaktoren kann eine zu messende Größe nicht völlig exakt erfasst werden. Die Abweichung einer Messung nennt man Messfehler oder auch Messabweichung.
Die Messanweisung legt die einzuhaltenden Bedingungen und den Ablauf des Messvorganges fest. Messanweisungen für rechnergestütztes Messen werden Messprogramme genannt.
Der Messbereich definiert den Teil oder die Teile des Anzeigebereichs für den oder für die die Fehler die vorgegebenen Fehlergrenzen nicht überschreiten.
Ein Messschieber mit dem Messereich 150 mm hat in der Regel einen Anzeigebereich der darüber hinausgeht. Messwerte die größer als 150 mm sind also ablesbar. Für diese Werte sind die Fehlergrenzen nicht mehr definiert.
Ein Messdorn ist eine besondere Art von Zylinderendmaßen. Im Unterschied zu den Zylinderendmaßen haben Messdorne Griff. Sie haben außerdem einen vordefinierten Nenndurchmesser und Sollabmaße, die sehr fein gestuft sein sollen. Was die zulässige Messabweichung betrifft, weisen die Messdorne unter den Endmaßen einen höheren Messgenauigkeitsgrad auf. Geringe Maß- und Formabweichungen sind das Auszeichnende bei den Messdornen.
Messen ist ein quantitativer Vergleich einer Messgröße bzw. einer zu messenden Größe mit einer als Einheit in Anspruch genommenen Bezugsgröße gleicher Art.
Der aus einer Messung gewonnene Messwert stellt häufig noch nicht das gewünschte Messergebnis dar. In vielen Fällen muss das Messergebnis erst durch eine weitere Errechnung aus einem oder mehreren Messwerten und zugleich unter besonderer Berücksichtigung der Messfehler gewonnen werden.
Grundsätzlich ist es nicht möglich exakt zu messen. Durch eine Vielzahl physikalischer Einflussfaktoren kann eine zu messende Größe nicht völlig exakt erfasst werden. Die Abweichung einer Messung nennt man Messfehler oder auch Messabweichung. In der Regel unterscheidet man in der Messtechnik zwischen systematischen und zufälligen Messfehlern.
Messgeräte oder auch Messinstrumente dienen zur Bestimmung geometrischer und physikalischer Größen welche in einer quantitativen Aussage über ein Messergebnis münden. Messgeräte zur Ausführung von Messungen zählen allgemein zur Gruppe der Messmittel. Werden diese zur Prüfung eingesetzt, werden sie auch als Prüfmittel bezeichnet.
Als Messgröße bezeichnet man nach DIN1319 zu den „Grundlagen der Messtechnik“, diejenige physikalische Größe als Messgröße, der eine Messung gilt. Physikalische Größen Können sein: Abstandsgrößen, Druckgrößen und weitere. In der Längenprüftechnik ist eine Messgröße in der Regel eine zu messende Länge/Breite/Höhe oder ein zu messender Winkel.
Mit Messkraft definiert man in der Messtechnik diejenige Kraft, die bei jeder Messung vom Messgerät bzw. von der Messeinrichtung ausgeht und die auf den zu messenden Gegenstand ausgeübt wird.
Die Messkraftumkehrspanne bezeichnet den Unterschied der Messkräfte, den man beim unverändert bleibenden Messwert erhält, wenn derselbe Messwert einmal bei steigenden und zum anderen mal bei fallenden Werten der Anzeige erreicht wird.
Informationen zur Herstellung von Messugeln:
Kugeln können aus beliebigen Materialien hergestellt werden. Der Herstellungsprozess für Präzisionskugeln unterscheidet sich im Wesentlichen nur in der geometrischen Ausgangsform des Rohlings. Die überwiegende Form des Rohlings ist der Draht für Metallkugeln, Stäbe bei gesinterten Werkstoffen (z.Bsp. Hartmetalle), Stahlkugeln < 30mm, Kunststoffkugeln und Glaskugeln. Andere Ausgangsformen sind Würfel oder gepresste sphärische Körper. Die Menge an verschiedene Kugelmaterialien und Qualitätsstufen hat zu einer Spezialisierung auf bestimmte Kugeln geführt. Im Zuge der Miniaturisierung hat sich z. B. die Firma Nanoball auf die Entwicklung und Herstellung von Miniaturkugeln konzentriert. Der Startschuss für die Miniaturisierung ist um das Jahr 1950 herum mit der Erfindung des Kugelschreibers gefallen.
Der Herstellungsprozess von Kugeln wird im Folgenden illustriert:
Der Ausgangsmetalldraht hat einen etwas größeren Durchmesser, als die zu fertigenden Kugeln. Der Draht wird kontinuierlich in einem Kaltumformungsprozess zunächst in kleine Zylinderstücke getrennt, die unmittelbar danach zwischen 2 halbförmigen Kalotten zu einer Kugel mit äquatorialem Ring zusammengestaucht werden. Dieser Prozess wird als Stauchen bezeichnet. Der zweite Bearbeitungsprozess, das sogenannte Flashen, dient zum Entfernen des Äquators. Hierzu werden die geschlagenen Rohlinge zwischen 2 Plangedrehte Schleifscheiben gebracht. Die Schleifscheiben sind entweder horizontal (Horizontalschleifmaschinen) oder vertikal (Vertikalschleifmaschinen) gelagert. Die untere Platte rotiert und die oberer Platte wird mit Druck auf die eingelegten Rohlinge gebracht. Unter Hinzugabe von Schmier,- und Schleifflüssigkeiten und Abrasiven (pulverförmige Schleifmedien, wie etwa Diamantpulver) wird der äquatoriale Ring abgerieben. Die entstandene Kugel hat nun eine sehr rauhe Oberfläche. Beim zweiten Schleifprozess, dem sogenannten Grobschliff, werden die Kugeln unter Hinzugabe von groben Schleifmitteln bis in Nähe des gewünschten Kugeldurchmessers geschliffen. Nach dem Grobschleifprozess erfolgt bei Stahlkugeln ein Härteprozess, um den Stahl mit der nötigen Härte zu versehen. Die nächsten Schleifprozesse werden auf verrillten Schleifplatten ausgeführt. Die Verrillung der Schleifplatten wird mit Hilfe einer Drehmaschine vorgenommen. Prinzipiell handelt es sich um zentrische Kugelbahnen, die zur definierten Führung der Kugeln zwischen den Schleifplatten dient. Die Kugeln laufen jeweils eine Umdrehung (360°) in einer Rille, und werden anschließend in eine weitere innere oder äussere Rille eingesetzt. Hierdurch wird erreicht, dass die Kugeln die geforderte Rundheit erlangen. Je nach vorgegebenem Genauigkeitsgrad (Güte Klasse), werden die Kugeln nach dem Härten in 2 – 3 weiteren, mit Rillen versehenen Schleifplatten bearbeitet. Die letzten Schleifprozesse unterscheiden sich dabei durch die Wahl der Schleifplattenmaterialien, den Abrasivestoffen und Schleifflüssigkeiten. Zwischen den einzelnen Schleifprozessen werden die Kugeln jeweils gewaschen, getrocknet und sortiert. Der Sortierprozess verhindert, dass fehlerhafte Kugeln den folgenden Schleifprozess stören könnten. Die Kugelschleifprozesse lassen sich wegen der Vielzahl an Schleifparametern (Schleifmaterialien, Schleifdruck und Schleifscheibenumdrehungszahl etc.) kaum automatisieren.
Güteklassen der Kugeln:
Die Kugeln werden in verschieden Qualitätsstufen eingeteilt. Eine internationale Norm (ISO 3290) vereint viele nationale Normen (z.B.:DIN 5401 Deutsche Norm, AFBMA Amerikanische Norm, JIS Japanische Norm). In den jeweiligen Normen werden die geometrischen Parameter der Kugel toleranzmäßig klassifiziert: Durchmessertoleranz, Rundheit, Formabweichung, Oberflächenrauhigkeit. Zusätzlich werden die Kugeln in Sorten eingeteilt. Die Sorteneinteilung spielt eine besondere Rolle bei Anwendungen in schnell drehenden Lagerungen.
Mit Messmethode beschreibt man eine spezielle Art der Durchführung einer Messung. Sie ist weder vom Messprinzip abhängig noch an der physikalischen Vollstreckung gebunden. In der Regel wird in der Messtechnik zwischen direkter und indirekter Messmethode unterschieden.
Ein Messmittel ist ein Hilfsmittel zur Ausführung einer Messaufgabe. Geräte zum Prüfen, Kalibrieren und Justieren sind ebenfalls Messmittel. Messmittel werden allgemeinhin auch als Prüfmittel bezeichnet.
Das Messprinzip bildet in der Messtechnik der physikalische Zusammenhang, der die Grundlage für eine Messung darzustellen hat.
Schematisierter Ablauf einzelner Prüfschritte. Kann auch mittels Software abgebildet werden.
Gute Messschieber bestehen aus gehärtetem nicht rostendem Stahl, um bei häufigem Gebrauch des Messschiebers den Abrieb zu mindern und die Maßhaltigkeit des Messschiebers dauerhaft zu gewährleisten. Daneben gibt es für geringere Anforderungen auch Messschieber aus Messing und Kunststoff. Messschieber für den Arbeitsbereich Metallbau haben meist auf der Rückseite eine eingravierte Tabelle, auf der den ganzzahligen Gewinde-Durchmessern die Durchmesser der zugehörigen Kernbohrer für die Vorbereitung zum Gewindeschneiden gegenübergestellt sind. Bei der Messung von Außen- und Innendurchmessern wird im Gegensatz zur Messschraube beim Messschieber das Abbesche Komparatorprinzip nicht eingehalten. Der dadurch bedingte Kippfehler 1. Ordnung führt zu einer im Aufbau des Messschiebers begründeten prinzipiell nicht vermeidbaren Messungenauigkeit. Weitere Fehlermöglichkeiten beim Messschieber sind Führungsfehler, Anlagefehler, an das zu messende Objekt, und Verschleiß (Beschädigung, Verschmutzung). Wenn mit der Tiefenmessstange gemessen wird, wird das Abbesche Prinzip jedoch nicht verletzt, da in diesem Fall Skala und Messstange in einer Flucht liegen. Das Messen mit dem Messschieber gehört zu den direkten Messverfahren, da Eingangsgröße und Ausgangsgröße identisch sind (in diesem Fall die Länge).
Aufbau eines Messschiebers
Messmöglichkeiten
Außenmessung
Innenmessung
Tiefenmessung
Stufen- / Abstandsmessung
Auszug aus DIN862 | |||
Fehlergrenzen G in μm bei Ablesung | |||
zu Messende länge(mm) | 0.1 / 0.05 mm | 0.02 mm | 0.01 mm |
50 - 100 | 50 | 20 | 20 |
100 - 200 | 50 | 30 | 30 |
200 - 300 | 50 | 30 | 30 |
300 - 400 | 60 | 30 | 30 |
400 - 500 | 70 | 30 | 30 |
500 - 600 | 80 | 30 | 30 |
600 - 700 | 90 | 40 | 40 |
700 - 800 | 100 | 40 | 40 |
800 - 900 | 110 | 40 | 40 |
900 - 1000 | 120 | 40 | 40 |
1000 - 1200 | 140 | 50 | - |
1200 - 1400 | 160 | 50 | - |
1400 - 1600 | 180 | 60 | - |
1600 - 1800 | 200 | 60 | - |
1800 - 2000 | 220 | 60 | - |
Messsignale nennt man in der Längenprüftechnik alle für eine Messung relevanten physikalischen Größen. Sie sollen für die Messung belangvolle Informationen enthalten.
Den messbaren Abstand zwischen dem Anfangswert und dem Endwert eines Messbereiches bezeichnet man in der Messtechnik die Messspanne.
Die grifflosen Messstifte sind Messkörper in zylindrischer Form. Sie haben in der Messtechnik ein sehr breites Anwendungsgebiet. Die wichtigsten industriellen Maßverkörperungen sind allerdings die Parallelendmaße.
Als Messsytem bezeichnet man die Gesamtheit von Messgerät bzw. Messmittel, Mensch und Umwelt. Aufgrund vielfacher physikalischer Einflussfaktoren ist es grundsätzlich nicht möglich fehlerfrei zu messen, d.h. eine Messgröße kann nicht fehlerfrei erfasst werden. Diese Abweichung vom tatsächlichen Wert der Messgröße bezeichnete man früher als Messfehler, heute verwendet man hierfür den Begriff der Messabweichung ( DIN 1319-1:1995 ).
Eine Messuhr ist ein Einbaulängenmessgerät mit Anzeige. Der vom Messbolzen beschrittene Weg wird durch ein mechanisches System, das in der Regel aus Zahnstange und Ritzel besteht, auf einen Zeiger, der auch Zahnradgetriebe genannt wird, übertragen und anschließend an einer Rundskale in vergrößerten Form angezeigt.
Auszug aus DIN 878
Messbereich mm | fe µm | fges µm | fw µm | fu µm |
0,4 | 7 | 9 | 3 | 3 |
0,8 | 7 | 9 | 3 | 3 |
3 | 10 | 12 | 3 | 3 |
5 | 12 | 14 | 3 | 3 |
10 | 15 | 17 | 3 | 3 |
Ziel einer Messung ist es, eine verlässliche Aussage über eine unbekannte Größe eines Objektes zu erhalten. Die Tätigkeiten sind dabei größtenteils praktischer Art, beziehen aber auch theoretische Überlegungen mit ein.
Ergebnis einer Messung ist der sogenannte Messwert. Dieser wird als Produkt einer Zahl und Maßeinheit dargestellt ( Siehe DIN 1313 ).
In einem ersten Schritt müssen vorhandene Messabweichungen mit bekannten systematischen Abweichungen verrechnet werden um so ein vollständiges Messergebnis zu erhalten.Das Messergebnis ist schließlich ein aus mehrfachen Messungen gewonnener Schätzwert. Diese Auswertung der Messungen bis zum angestrebten Ergebnis ist Teil der Messaufgabe, eine weitere Verwendung der Messergebnisse, wie beispielsweise das Prüfen oder Regeln, gehört nicht mehr dazu.
Die Messunsicherheit geht über eine Eignungsanalyse hinaus. Bei ihr wird jedem Messwert eine Info hinzugefügt, wie zuverlässig das angezeigte Ergebnis ist, besser gesagt wie unzuverlässig. Für die Ermittlung wird versucht alle Einflussgrößen, etwa Temperaturschwankungen mit den daraus resultierenden Längenänderungen zu erfassen und aufzuschlüsseln. Anschließend erfolgt eine Abschätzung inwiefern sich die Faktoren auswirken, wobei für jede Größe eine statistische Verteilung erstellt wird. Die statistische Verteilung ermmöglicht die Errechnung einer maximalen Messunsicherheit, die angibt in welchem Wertebereich um den gemessenen Wert herum der wahre Wert voraussichtlich liegen wird. Die Angabe der Messunsicherheit gibt also an, inwiefern man dem ermittelten und angezeigten Werten vertrauen kann.
Wenn ein Messprinzip und eine Messmethode gemeinsam in die praktische Anwendung kommen, ergibt sich hier ein Messverfahren. Häufig unterscheidet man in der Messtechnik zwischen direktem, indirektem, analogem und digitalem Messverfahren.
Ein Messwert ist die aus einer Messung sich ergebende quantitative Aussage über die Messgröße eines Prüfgegenstandes; er besteht aus dem Zahlenwert und der Einheit, z. B. 30 m. Der Messwert ist mit dem wahren Wert der Messgröße nicht gleichzusetzen. Zu berücksichtigen ist noch die Messunsicherheit. Vom Messergebnis muss der Messwert ebenfalls unterschieden werden.
Messwertumkehrspanne eines anzeigenden Messgerätes bezeichnet den Unterschied der Anzeigen, den man beim unverändert bleibenden Wert der Messgröße erhält, wenn die Messung einmal bei steigenden und ein andermal bei fallenden Werten der Anzeige durchgeführt wird.
Eine Messwertverarbeitung wird in Anspruch genommen, wenn die ursprünglich erzielte Messgröße dem Messergebnis nicht unmittelbar entgegenkommt. Man unterscheidet in der Messtechnik zwischen elementarer und höherer Messwertverarbeitung.
Flankenwinkel 60°
Toleranzen Regelgewinde und Feingewinde
Übersicht für Gewinde-Lehrringe
4h | Toleranzklasse „fein“ |
6h | Toleranzklasse „mittel“, für kleine Abmessungen (bis M 1,4) |
6g | Toleranzklasse „mittel“ - Standard |
6e | Untermaß-Toleranz; Gewindelehren mit 6e-Toleranz sind ca. 0,03 mm kleiner als mit Standardtoleranz 6g. |
8e | Untermaß-Toleranz; |
Übersicht für Gewinde-Lehrrdorne
4H | UntermaßGewindeverbindungen mit wenig Spiel |
6h | Toleranzklasse „mittel“, für kleine Abmessungen (bis M 1,4) |
6g | Toleranzklasse „mittel“ - Standard |
6e | Untermaß-Toleranz; Gewindelehren mit 6e-Toleranz sind ca. 0,03 mm kleiner als mit Standardtoleranz 6g. |
8e | Untermaß-Toleranz; |
Metrisches ISO Gewinde DIN 13 | ||||
M | Außen-Ø in mm | Steigung P in mm | Umrechnung: Gänge je Zoll | Umrechnung: Außen-Ø in Zoll |
M 1 x 0,25 | 1 | 0,25 | 0,039 | 101,6 |
M 1,1 x 0,25 | 1,1 | 0,25 | 0,043 | 101,6 |
M 1,2 x 0,25 | 1,2 | 0,25 | 0,047 | 101,6 |
M 1,4 x 0,3 | 1,4 | 0,3 | 0,055 | 84,667 |
M 1,6 x 0,35 | 1,6 | 0,35 | 0,063 | 72,571 |
M 1,8 x 0,35 | 1,8 | 0,35 | 0,071 | 72,571 |
M 2 x 0,4 | 2 | 0,4 | 0,079 | 63,5 |
M 2,2 x 0,45 | 2,2 | 0,45 | 0,087 | 56,444 |
M 2,5 x 0,45 | 2,5 | 0,45 | 0,098 | 56,444 |
M 3 x 0,5 | 3 | 0,5 | 0,118 | 50,8 |
M 3,5 x 0,6 | 3,5 | 0,6 | 0,138 | 42,333 |
M 4 x 0,7 | 4 | 0,7 | 0,157 | 36,286 |
M 4,5 x 0,75 | 4,5 | 0,75 | 0,177 | 33,867 |
M 5 x 0,8 | 5 | 0,8 | 0,197 | 31,75 |
M 6 x 1,0 | 6 | 1 | 0,236 | 25,4 |
M 7 x 1,0 | 7 | 1 | 0,276 | 25,4 |
M 8 x 1,25 | 8 | 1,25 | 0,315 | 20,32 |
M 9 x 1,25 | 9 | 1,25 | 0,354 | 20,32 |
M 10 x 1,5 | 10 | 1,5 | 0,394 | 16,933 |
M 11 x 1,5 | 11 | 1,5 | 0,433 | 16,933 |
M 12 x 1,75 | 12 | 1,75 | 0,472 | 14,514 |
M 14 x 2,0 | 14 | 2 | 0,551 | 12,7 |
M 16 x 2,0 | 16 | 2 | 0,63 | 12,7 |
M 18 x 2,5 | 18 | 2,5 | 0,709 | 10,16 |
M 20 x 2,5 | 20 | 2,5 | 0,787 | 10,16 |
M 22 x 2,5 | 22 | 2,5 | 0,866 | 10,16 |
M 24 x 3,0 | 24 | 3 | 0,945 | 8,467 |
M 27 x 3,0 | 27 | 3 | 1,063 | 8,467 |
M 30 x 3,5 | 30 | 3,5 | 1,181 | 7,257 |
M 33 x 3,5 | 33 | 3,5 | 1,299 | 7,257 |
M 36 x 4,0 | 36 | 4 | 1,417 | 6,35 |
M 39 x 4,0 | 39 | 4 | 1,535 | 6,35 |
M 42 x 4,5 | 42 | 4,5 | 1,654 | 5,644 |
M 45 x 4,5 | 45 | 4,5 | 1,772 | 5,644 |
M 48 x 5,0 | 48 | 5 | 1,89 | 5,08 |
M 52 x 5,0 | 52 | 5 | 2,047 | 5,08 |
M 56 x 5,5 | 56 | 5,5 | 2,205 | 4,618 |
M 60 x 5,5 | 60 | 5,5 | 2,362 | 4,618 |
M 64 x 6,0 | 64 | 6 | 2,52 | 4,233 |
M 68 x 6,0 | 68 | 6 | 2,677 | 4,233 |
Bereits über 305.000
zufriedene Kunden!
Mitglied der Initiative
"Fairness im Handel".
fairness-im-handel.de